Zhongchen Light Machinery's 40,000BPH High-Speed Beer Filling Line has been successfully put into operation at AB InBev
Horses gallop into the New Year, triumphant songs bid farewell to the old one. Following the successful commissioning of a 40,000BPH high-speed beer/beverage combination production line at Carlsberg's global headquarters, Zhongchen Light Machinery began the New Year by successfully launching a 40,000BPH beer production line at the Suqian factory of Budweiser Anheuser-Busch, another heavyweight hit after seven collaborations with Budweiser Anheuser-Busch.
AB InBev is a Fortune 500 company and ranks third in the global fast-moving consumer goods industry and first in the global beer industry. With a history of over 100 years, AB InBev, the brewing group with a long history, owns global flagship beer brands such as Budweiser, Stella Artois, and Beck's, and its business covers more than 30 countries and regions. It has over 100 factories globally, including more than 40 in China. It invested 2.7 billion yuan to build the North China (Suqian) Beer Production Base Project, which has an annual output of 1 million tons, mainly producing Budweiser and Harbin, two famous brands of AB InBev. The project undertaken by Zhongchen Light Industry Machinery includes the washing machine, filling machine, and sterilization machine, the three main host equipment of the 40,000BPH high-speed beer filling production line, as well as the 4-can automatic CIP cleaning system.

Zhongchen Light Industry Machinery supplies a double-end deep groove washing machine for this project, with the inlet and outlet ends being separate, achieving separation of dirty and clean bottles and reducing the risk of contamination of clean bottles; the main transmission uses a SEW variable-speed motor, which can be adjusted in speed through frequency conversion, and the in-and-out bottle transmission is synchronized with the main transmission through the electrical system; the machine is equipped with multiple overload safety protection devices to ensure safe and stable production; the machine is equipped with 3.5 continuous alkali soaking tanks, each with a full plastic bottle holder arranged in 47 rows, achieving a high alkali soaking time of nearly 20 minutes; the liquid temperature in each soaking tank can be set and controlled automatically, the liquid level is fully automatically controlled, and an automatic alkali addition system is provided to achieve online alkali addition; the machine is equipped with a full rotary spray design, which can control the diameter and number of new water spray holes, the flow rate and pressure of new water, and multiple water circulation utilization, achieving a measured water consumption that is more than 50% lower than that of traditional washing machines; moreover, an efficient chain net de-labeling system is provided for each alkali tank, which is combined with an online label crushing machine, greatly improving the environment in the production area; the machine is also equipped with the most rigorous safety protection design, fully meeting the international safety protection standards. Since production, the key indicators of machine efficiency, cleanliness rate, breakage rate, steam consumption, and water consumption have all met the requirements of AB InBev and have been highly recognized by the project team and the factory.
The filling machine is equipped with a combination of 128 nozzle filling valves and 22 capping heads. The whole machine design adopts a cleaning table version, with a front lift-up door, providing a clear view and making operation easier. It uses high-precision mechanical filling valves or semi-electronic valves, which have the function of no filling without bottles and no vacuuming. It is equipped with an imported high-pressure foaming device that uses fine stream hot sterile water (85°C) to foam, and the foaming pressure is synchronized with the host speed for gradual adjustment. It is equipped with a Nasim vacuum pump with a circulating water temperature control device to ensure vacuum degree. The CIP cleaning cup realizes automatic circulating cleaning of the filling machine. The machine's pipe station is equipped with high-standard filtering, detection, and control devices, including wine intake, CO2 intake, and compressed air intake. The magnetic cover feeding machine and capping machine are fully interlocked, ensuring highly reliable capping performance. The equipment is equipped with an automatic CIP cleaning system, which can be used for both regular beer line cleaning and pure beer line cleaning. Since the machine has been running, the overall efficiency, TPO, net capacity, beer loss, lid loss, and CO2 consumption have all met or exceeded the standard requirements of InBev.
The sterilizer adopts a double-layer, dual-channel, open stainless steel wall structure with centralized heating; the temperature gradient is small, which can ensure good sterilization effects while reducing the breakage rate; it uses multiple stages of circulating warm water pre-cooling, circulating hot water spray sterilization, and circulating cold water cooling to achieve stable in-machine thermal balance and save water and heat; at the same time, it uses high-efficiency, easy-to-remove spray nozzles, with water consumption measured at less than 1.5-2 tons per hour; it is equipped with Zhencheng Light Machinery's proprietary high-end PU value real-time control system, with temperature control accuracy of +/- 0.5℃ and minimal fluctuations in the upper and lower layer PU values.
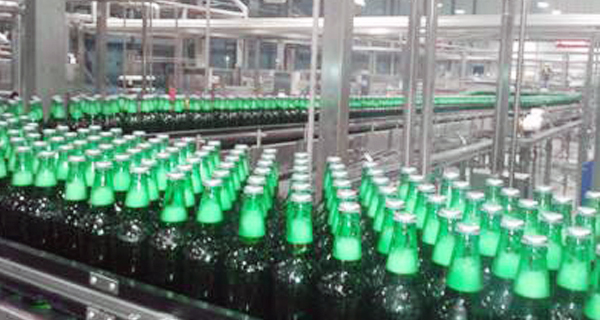
The successful commissioning of the 40,000BPH high-speed production line for Budweiser InBev beer in Suqian marks another milestone for Zhongchen Light Industry Machinery, standing at the pinnacle of the high-speed beer filling and packaging industry. Zhongchen Light Industry Machinery has also launched the three main equipment of the 50,000BPH high-speed beer glass bottle production line in early 2014, which will undoubtedly write a brilliant chapter in the development of China's independent brand high-speed beer packaging production line. At the same time, the cooperation with Budweiser InBev is another win-win cooperation after Zhongchen Light Industry Machinery's cooperation with Carlsberg, Heineken, Wahaha, PepsiCo, and Coca-Cola, etc., international beer and beverage giants, in the high-speed production line. It will further enhance Zhongchen Light Industry Machinery's brand image and value, and Zhongchen Light Industry Machinery will continue to make outstanding contributions to the development of beer and beverage filling and packaging equipment industry in China and overseas with its innovative technology, high-quality products, and efficient services.
2013 was a year of dreams and glory shining brightly. 2014, we set sail again, embarking on a new journey!
Recommended News
-
ABInBev Group visited Zhongchen Light Machinery
2025-03-15
-
Good News |Hefei ZhongChen(HF.ZCQJ)Honored with Carlsberg Group's "Outstanding Supplier" Title
2025-05-13
-
CBST 2025 Successfully Concludes: Zhongchen Light Machinery Shines on the "Digital, Intelligent, and Green" Stage
2025-03-07
-
CBST 2025 Successfully Concludes: Zhongchen Light Machinery Shines on the "Digital, Intelligent, and Green" Stage
2025-03-07
-
Fun Welcoming the New Year | Exciting and Thrilling! Zhongchen Light Machinery’s Sports Event Was a Blast!
2025-01-20
-
The governor of Anhui Province, Wang Qingxian, visited Zhongchen Light Machinery to investigate its digital transformation progress.
2024-12-10
-
CBB 2024 | Zhongchen Light Machinery Makes a Grand Appearance!
2024-11-27
-
CBB 2024 | Zhongchen Light Machinery Makes a Grand Appearance!
2024-11-27
-
"Eight Good" Goals Accelerate Implementation | Budweiser Equipment Supplier Strategic Alliance - Zhongchen Light Machinery & Budweiser Xinxiang VPO Launch Conference
2024-11-13
-
Zhongchen Light Machinery and CCH Coca-Cola Strategic Cooperation Kicks Off
2024-09-19